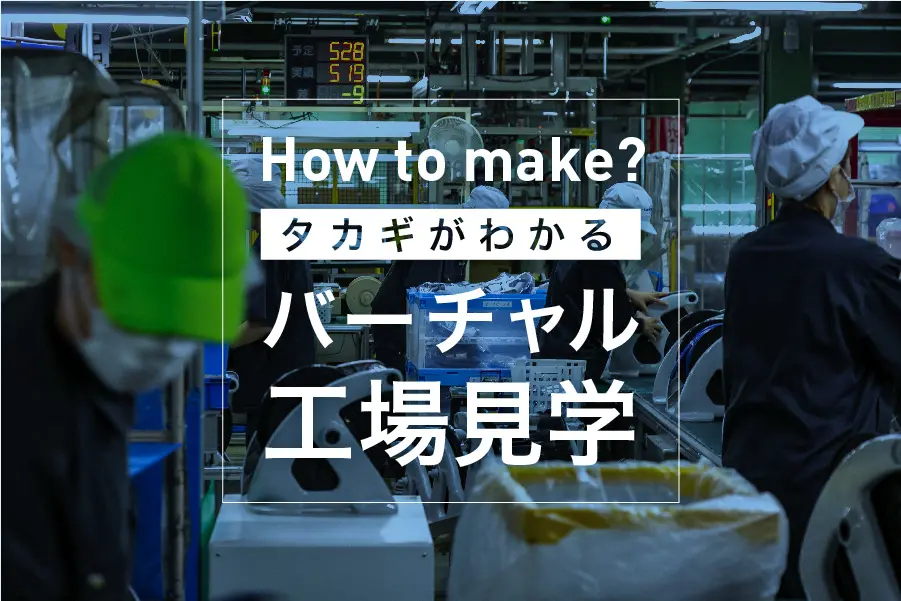
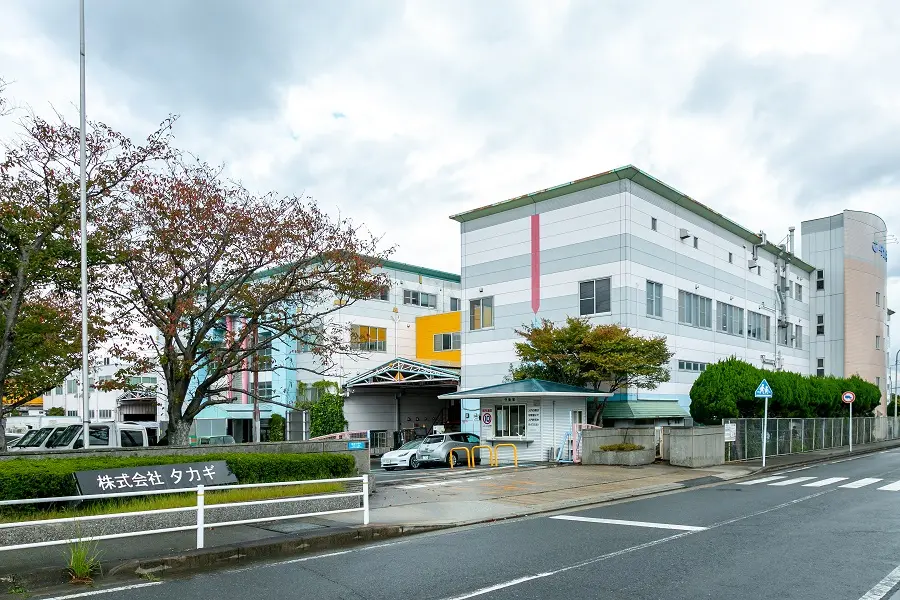
本社の外観。ここからタカギの歴史は始まりました。
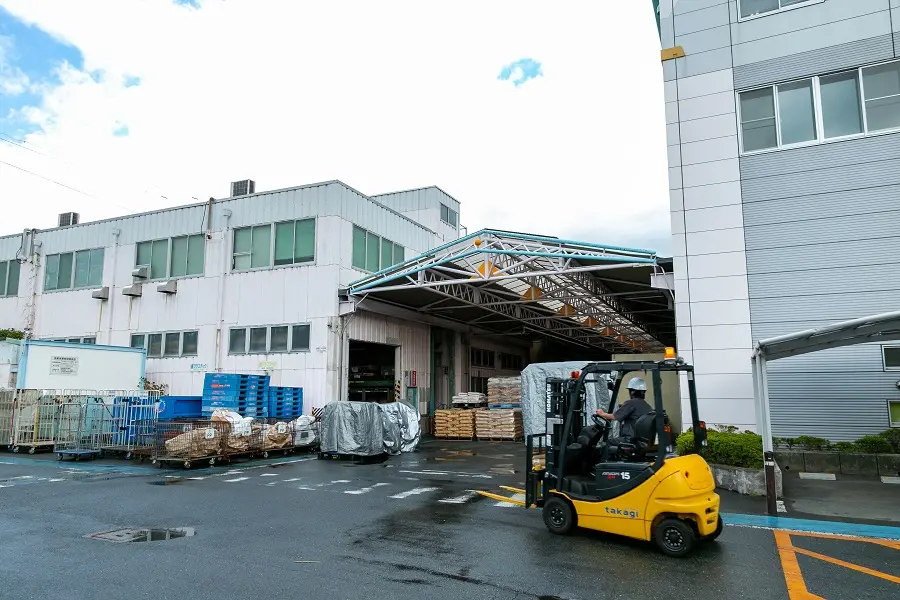
工場はフォークリフトやトラックが行き交い、いつも活気ある雰囲気です。
工場内には、タカギの歴史や過去の製品ラインアップ、蛇口一体型浄水器の製造工程などが紹介されている「ミニミュージアム」があります。ここにはタカギを象徴する広告が展示されています。
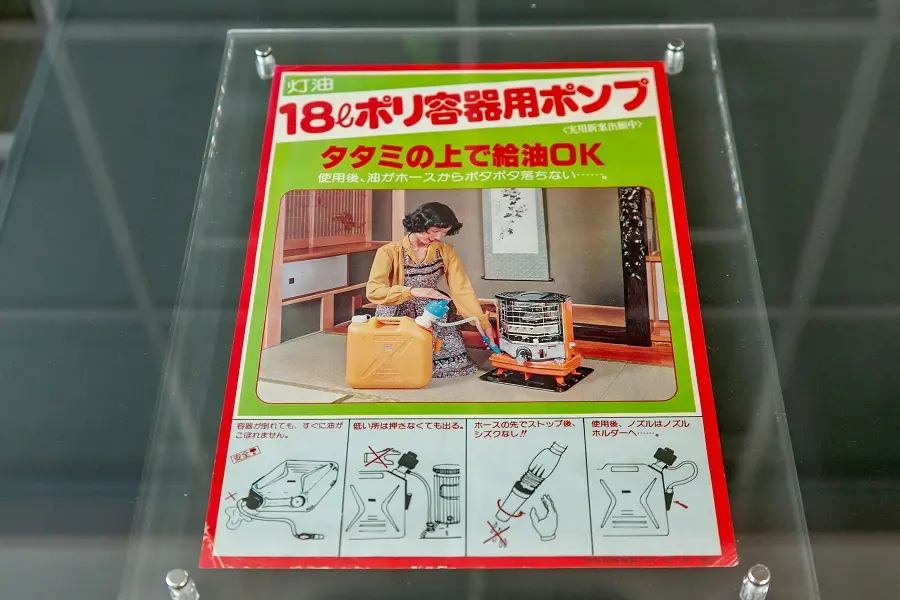
展示でひと際目立つ広告は当時大きな話題となりました。
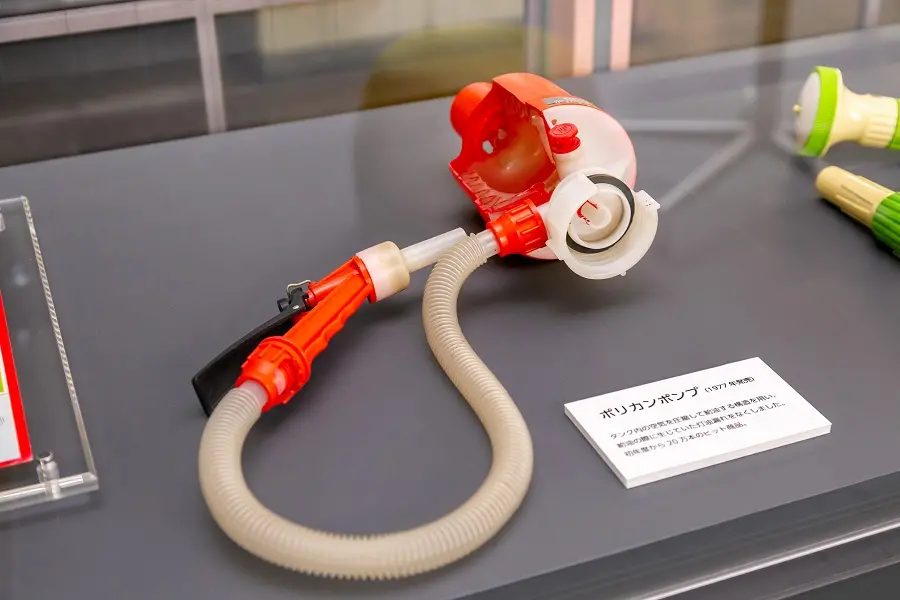
ポリカンポンプはお客様に寄り添うものづくりの原点です。
ポリカンポンプはその悩みを解消しました。タンクにポンプをつけっぱなしにでき、倒れても油がすぐに出ないことがお客様の心をつかみました。100円ポンプの時代に、1980円のポンプが累計20万本販売され、多くのお喜びの声をいただきました。お客様に寄り添うタカギの製品づくりは、ここから始まりました。(ポリカンポンプは今も発売中です!)
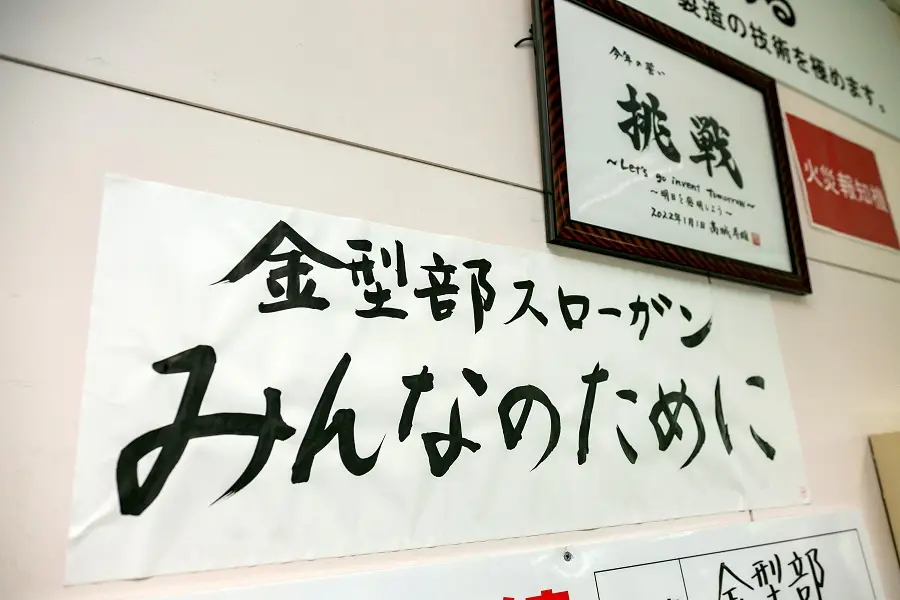
タカギが大事にするものづくりへの思いが壁一面に貼られています。
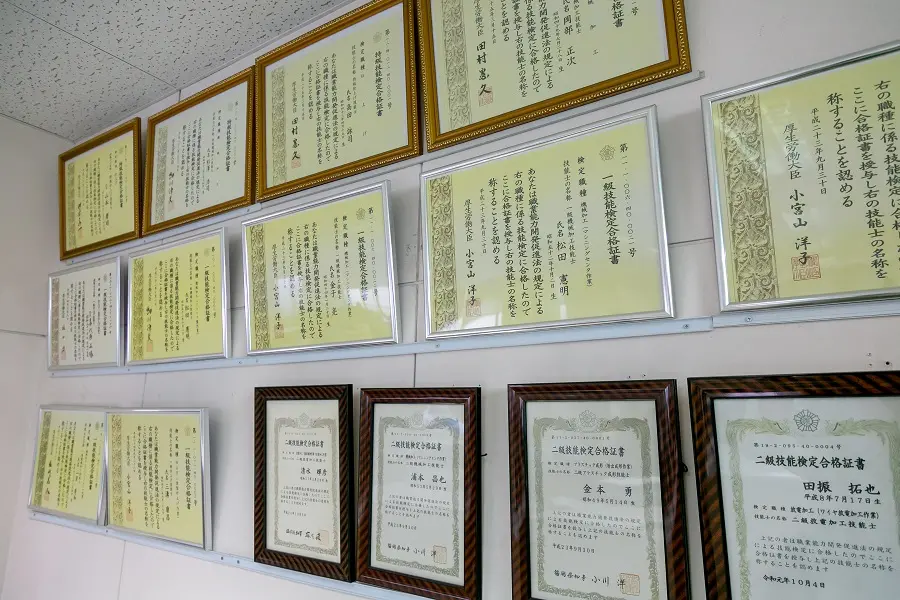
タカギの技術者が持つ資格の数々。
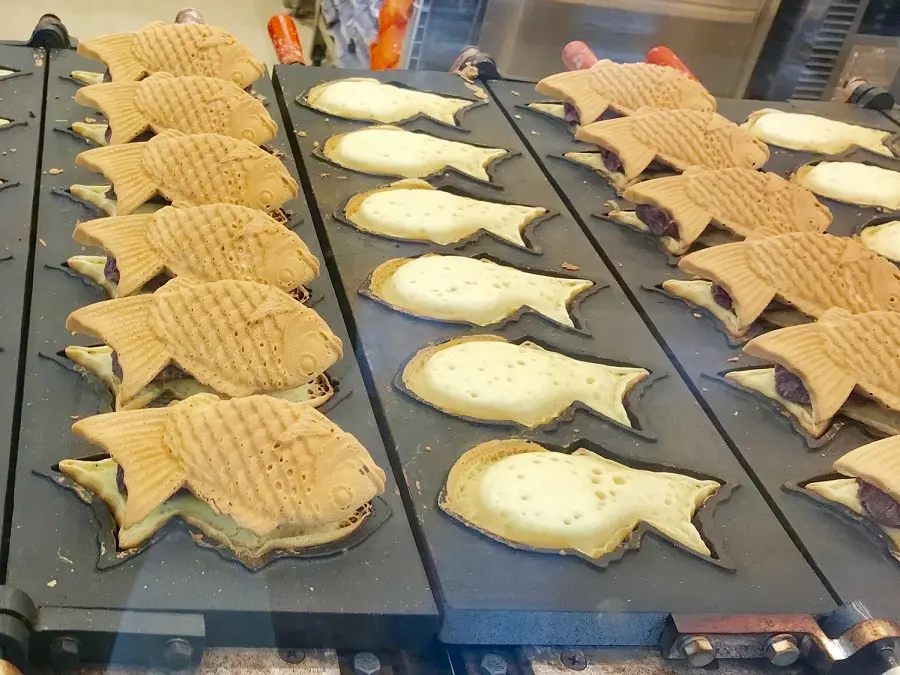
突然のタイ焼き!?でも実は金型で作られています。
※あくまで身近にある「金型」の例になります。タカギではタイ焼きの金型は製造しておりません。
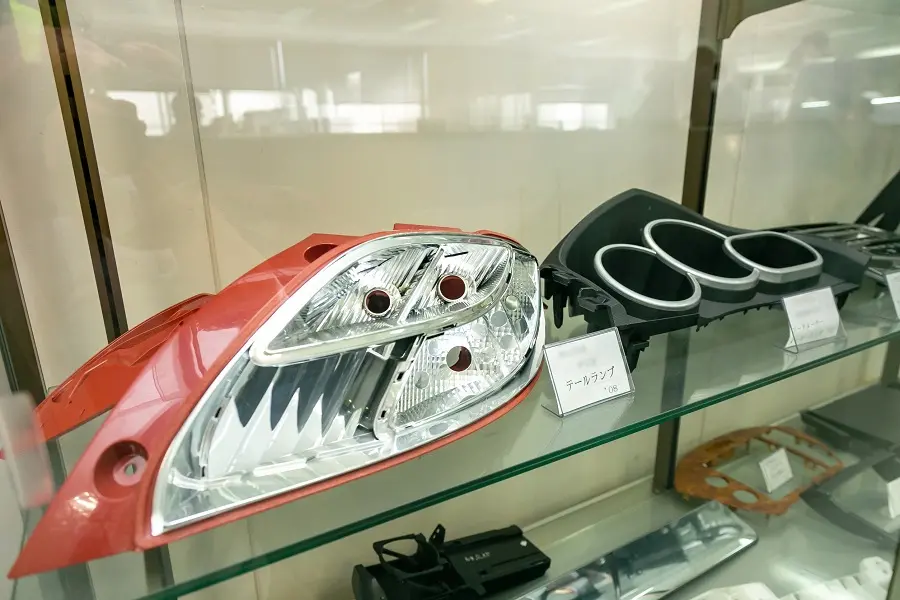
タカギでは実に10トンもある大型の金型まで対応しています。
家電・通信機器・日用品向けでは、生活に馴染みがある商品の金型を多く作っています。赤ちゃん用のスプーン&フォークや殺虫剤のノズル部分を作るための金型なども手掛けています。
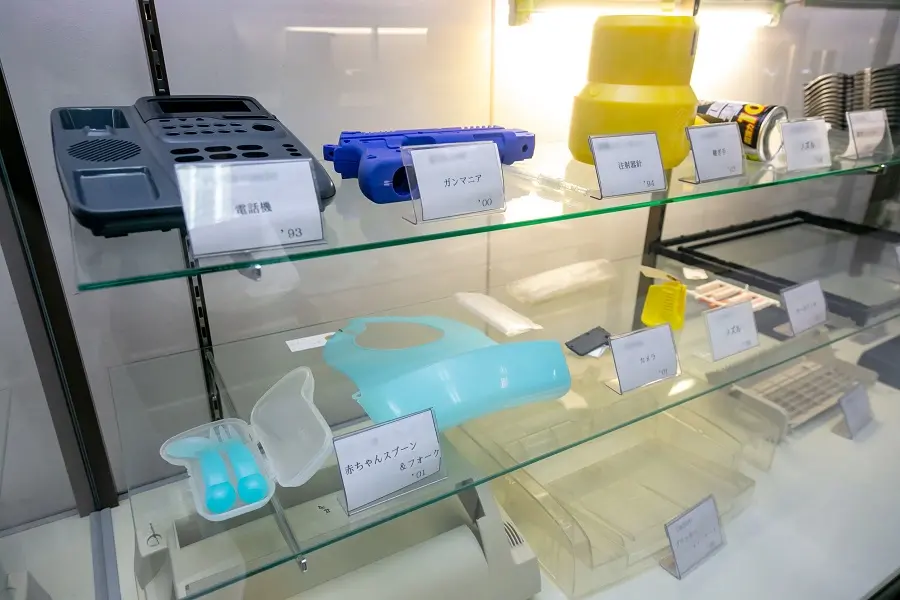
プリンタや電話機など、あなたの身近にある製品には金型が不可欠です。
この金型技術はタカギの製品づくりにも活きています。例えば、散水用品や浴室用シャワーヘッド。きめ細やかなシャワーを生み出すには、微細な穴が不可欠です。ここでも熟練の金型技術が活躍します。
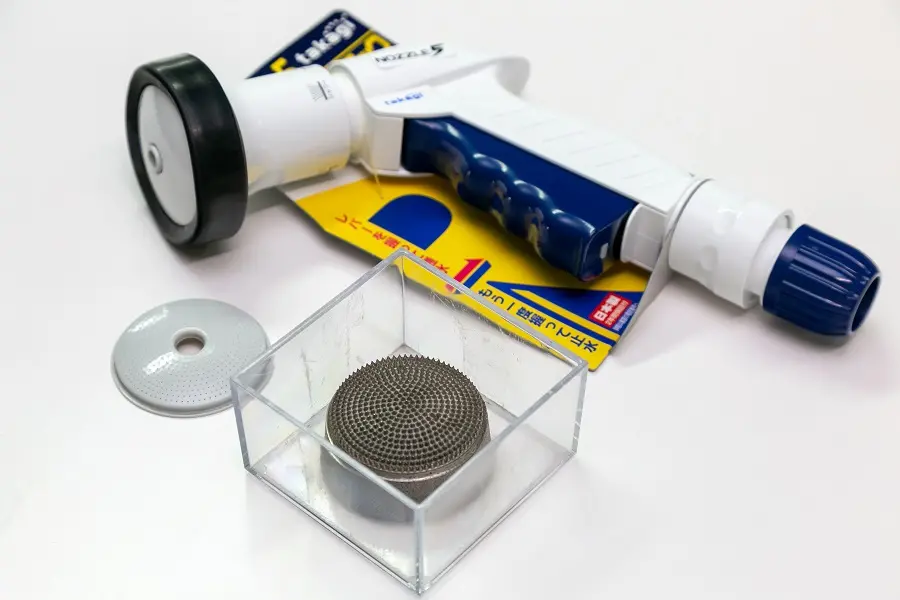
高精度な金型製作はタカギのものづくりの下支えとなっています。
金型が磨かれていれば、つるつるの綺麗な面を作り出すことができます。成形品を作る際には、樹脂が飛び出して余分な部分ができます。これをバリといいますが、削るのに手間がかかります。良い金型を使うとバリがほとんどできないので、後工程を減らすことに貢献します。蛇口一体型浄水器の部品用の金型でも、こうした高い技術が活きています。
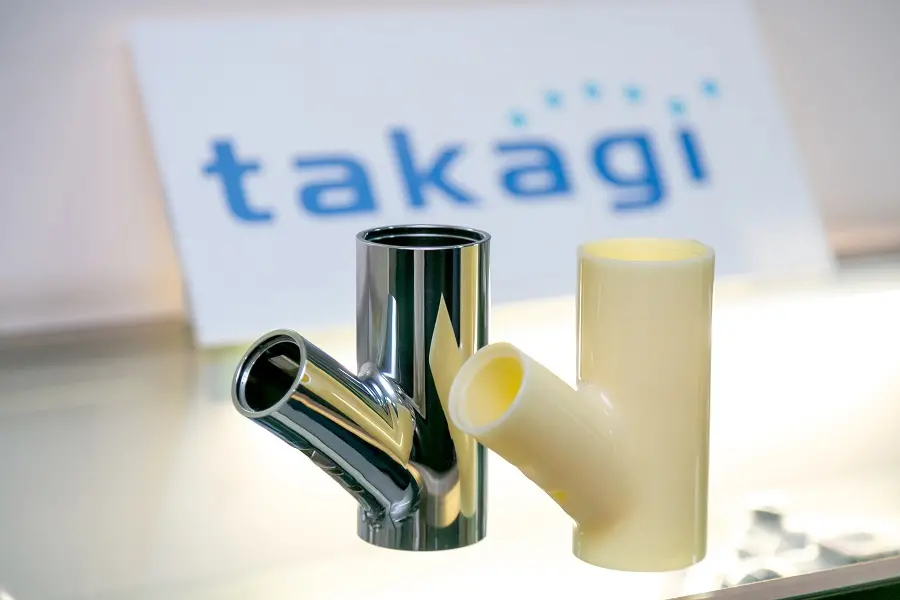
壊れずに長く使い続けられる金型製作ができるのもタカギの強みです。
金型技術者は、1/1000mmの精度に挑むといわれます。長い歴史と経験で積み上げられた金型技術だからこそ、ものづくりをスピーディーかつ柔軟に行うことができます。
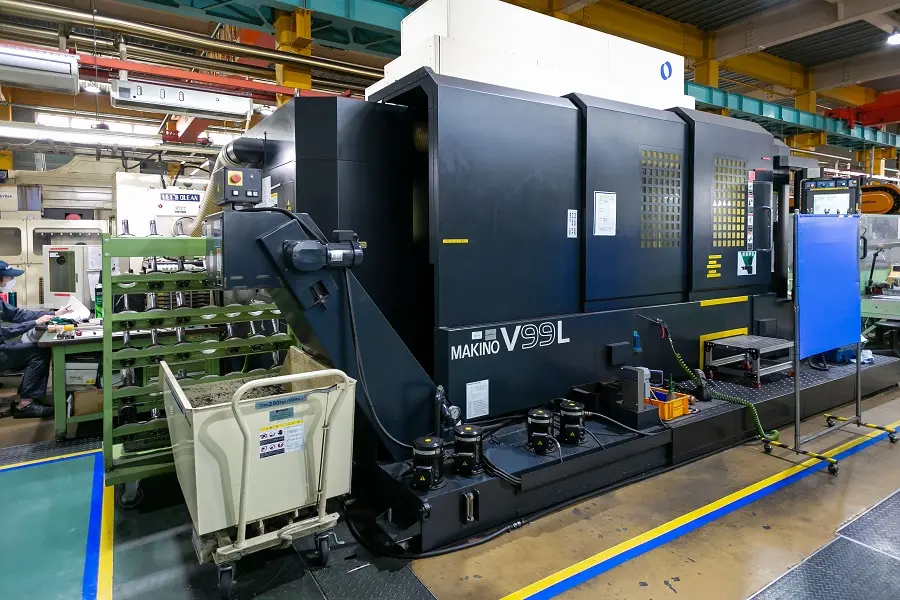
最新鋭の機械は、複雑で微細な部品加工も可能にします。
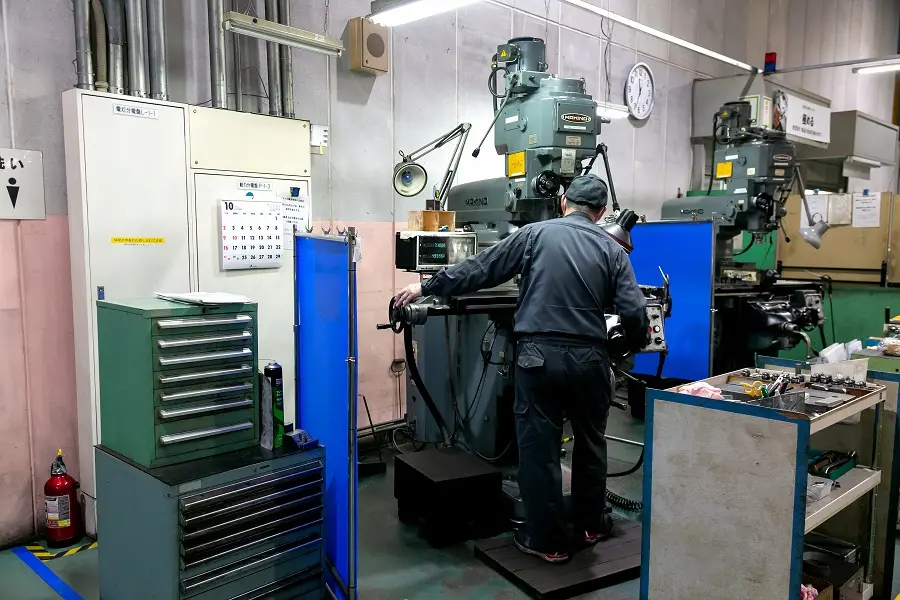
金型づくりには信頼出来る技術者の存在が欠かせません。
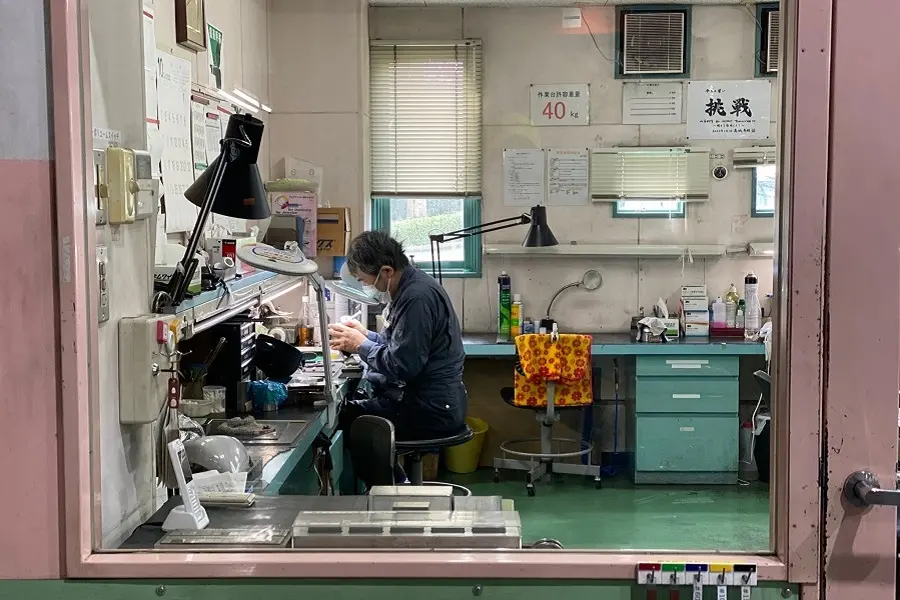
最後の仕上げは、匠の手で行います。
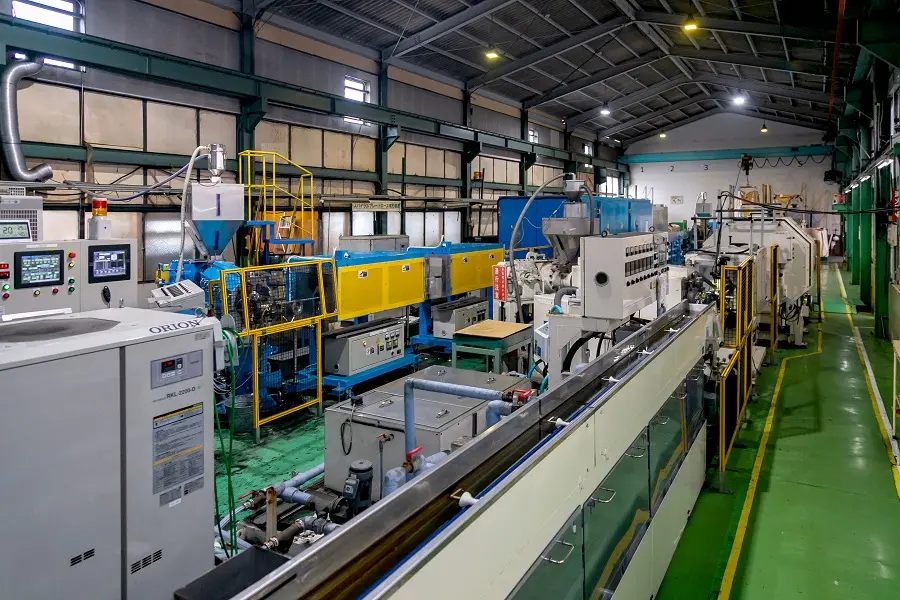
押出成形は合成樹脂に対する成形加工の中でも特に量産性に優れた方法といわれています。
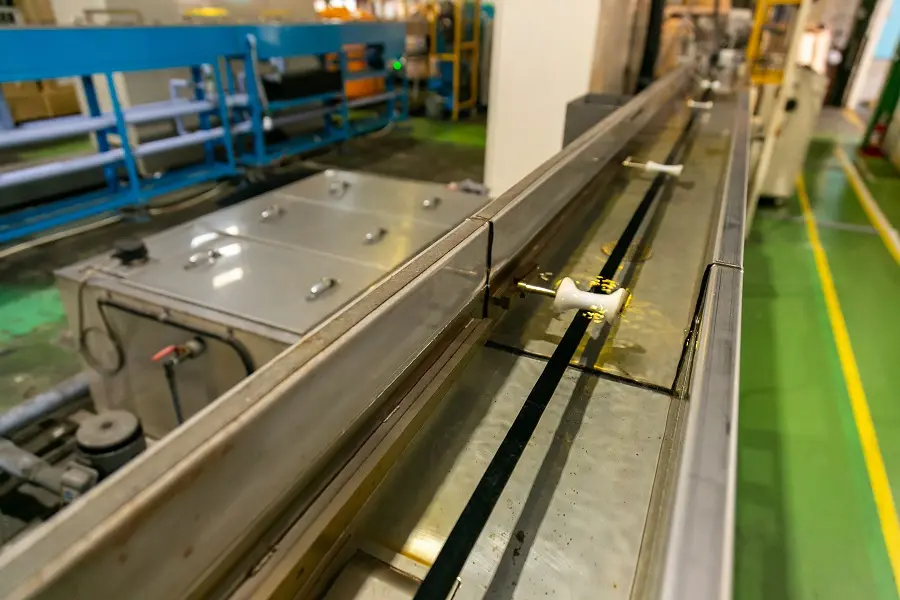
樹脂を押し出した後、水で急速に冷却する様子。
インナーとなる樹脂が押し出されたあと、糸が巻かれ、その後色付きの樹脂を被せる工程を経て、私たちが普段見るホースの姿になっていきます。
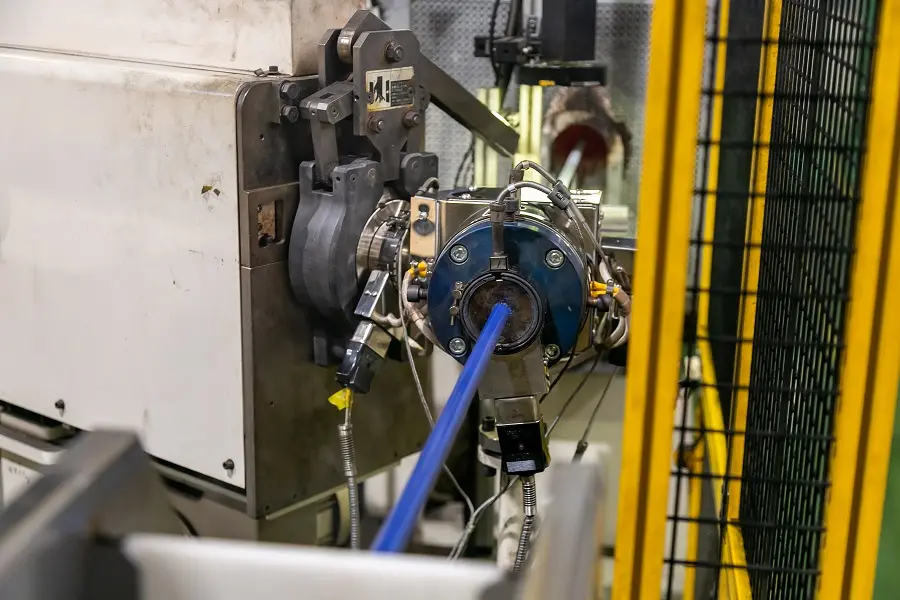
色付けされ、巻かれていくと製品のベースが完成です。
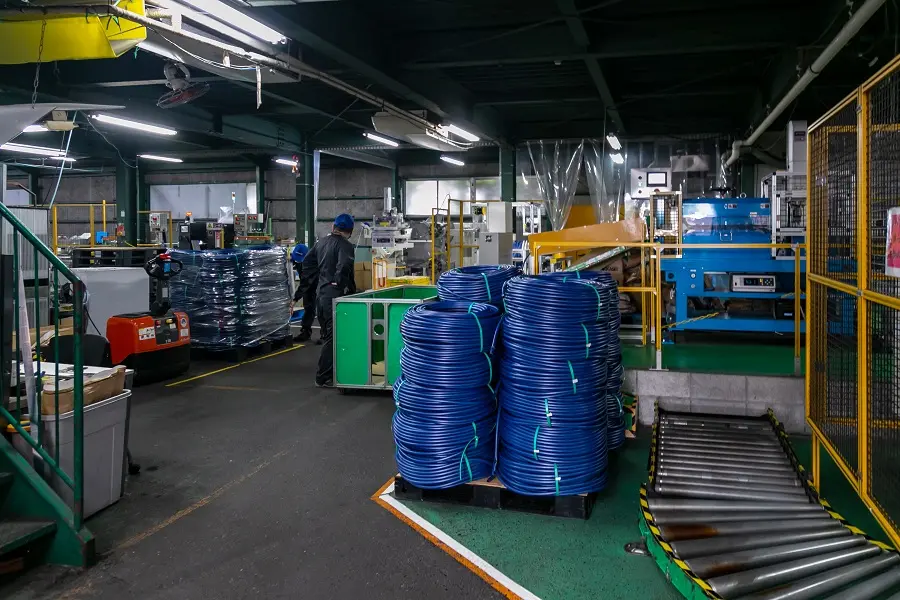
ホースの束が積み上がる様子は圧巻。
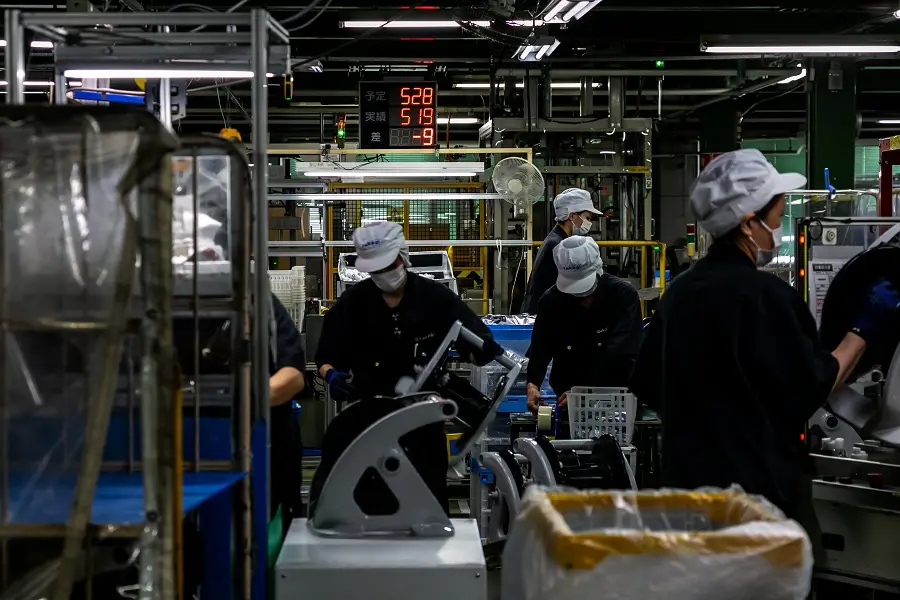
現場では、性別、国籍、年齢など多様な人材が活躍しています。
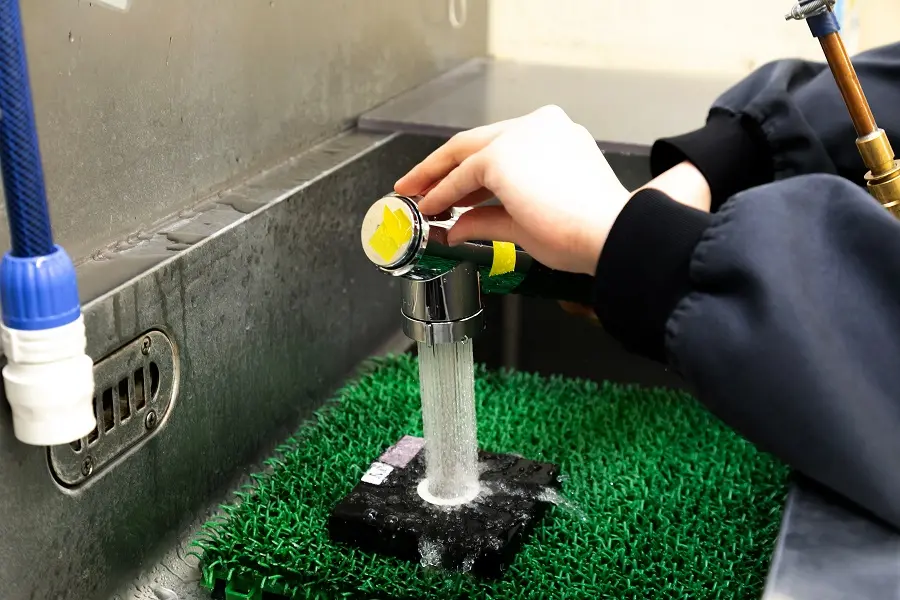
シャワーとストレートの切り替えを何度も行うなど、念入りにチェックされていきます。
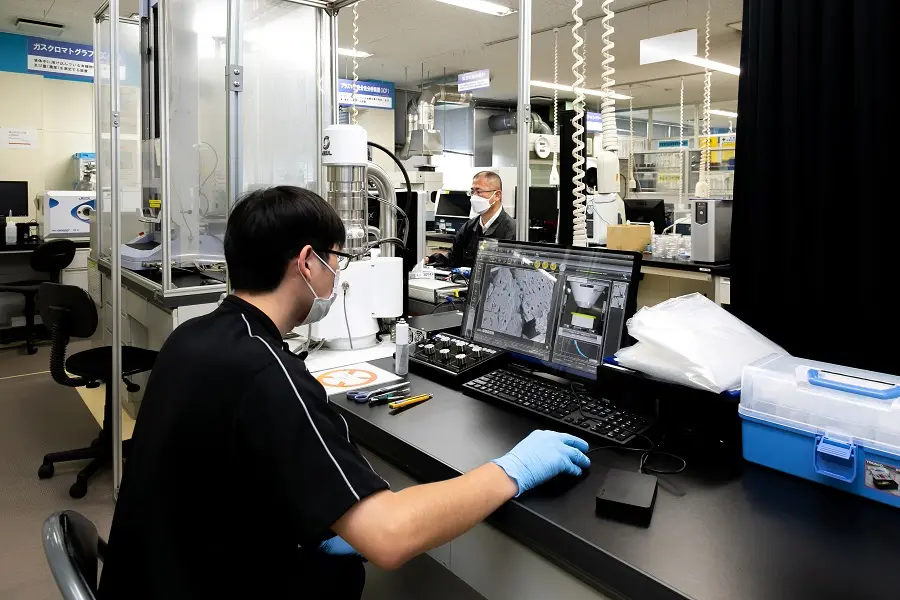
高倍率観察ができる電子顕微鏡は医療分野などでも活躍しています。
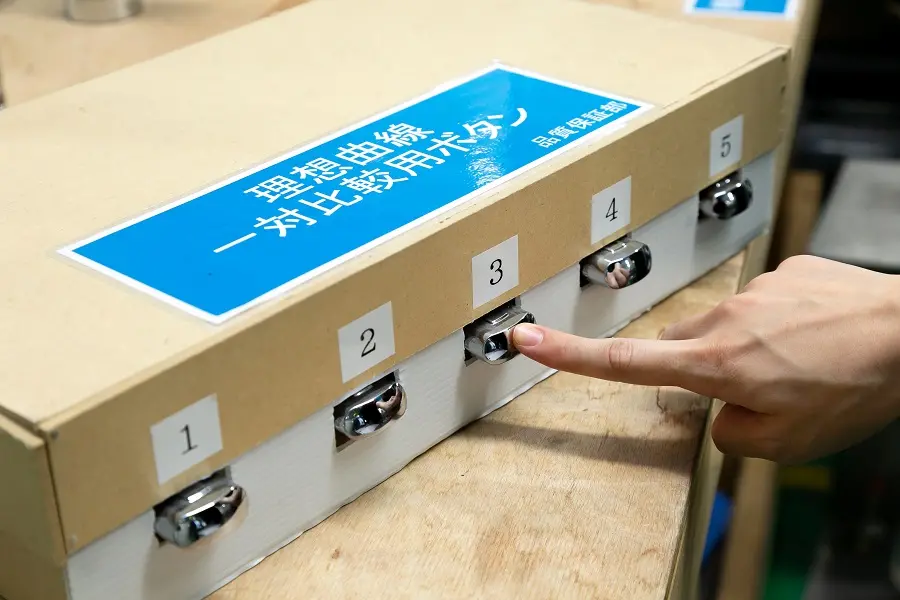
常にお客様の気持ちに立ち「理想の製品」を目指しています。
評価試験センターの一角には、台所やバスルームが再現された場所もあります。時には料理をして蛇口一体型浄水器の操作性を検証したり、シャワーヘッドをバスルームで体感したりすることも。お客様に安心・安全の製品をお届けするために、評価試験センターではこれからも検証・研究に努めます。
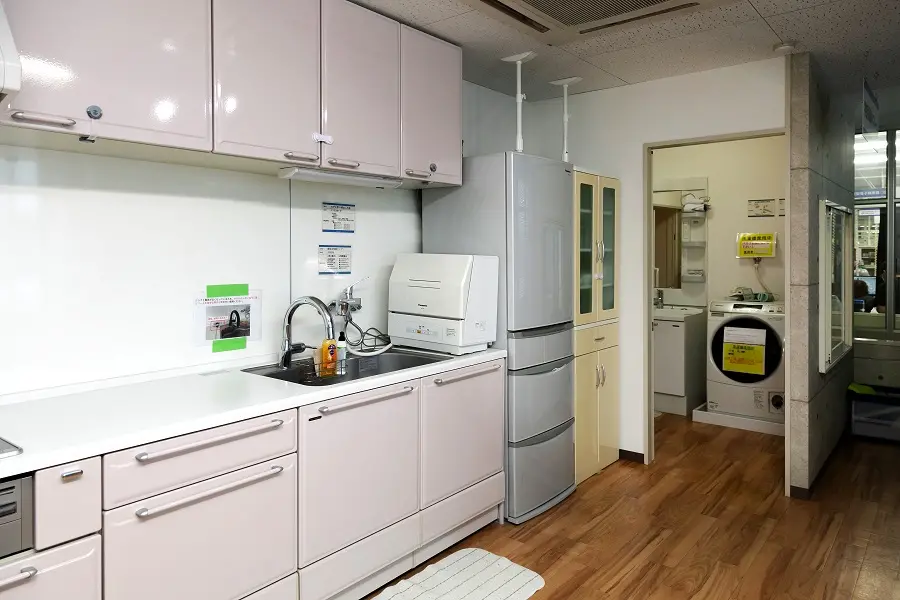
実際に製品を体感することも、ものづくりの大事なアプローチです。
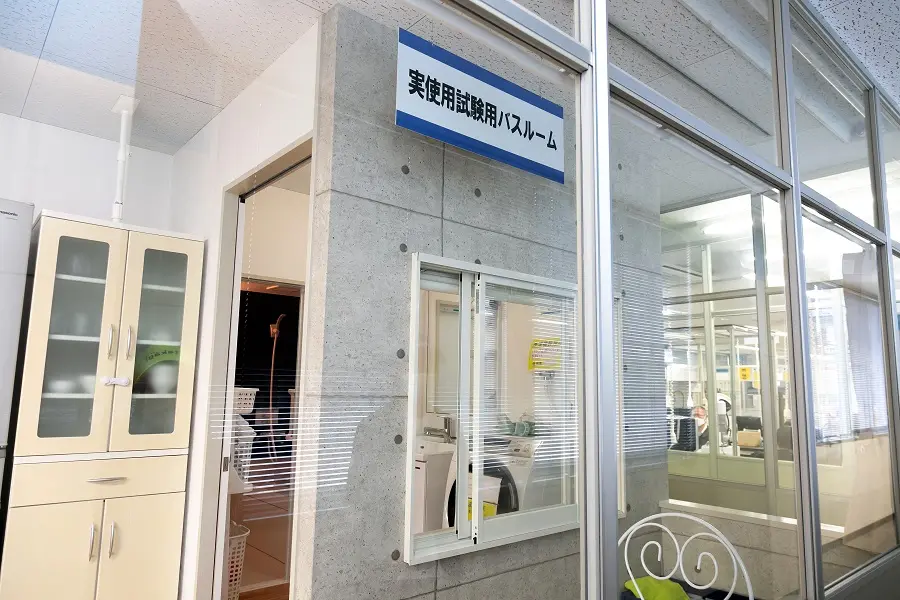
工場内にある試験用のバスルームやキッチン。
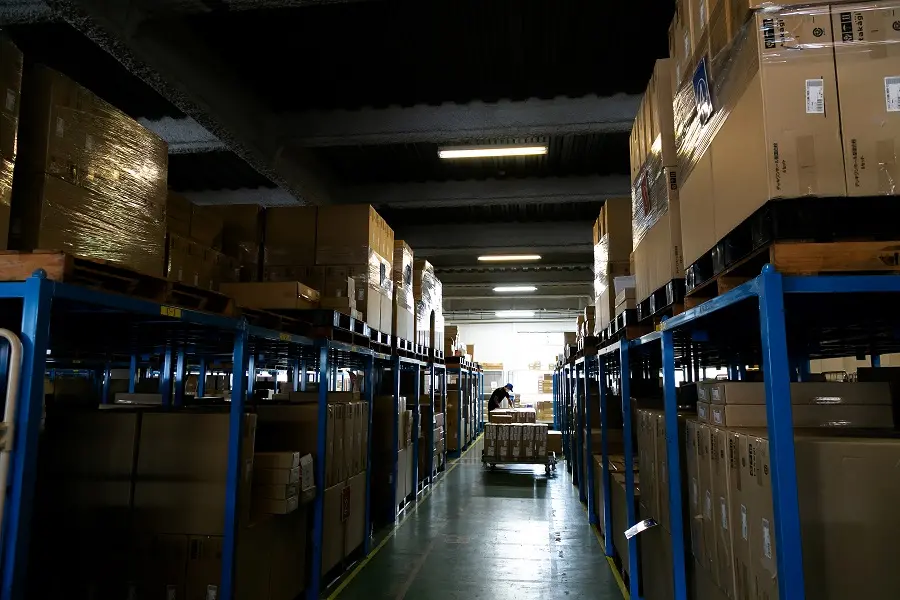
工場内にある物流倉庫の様子。
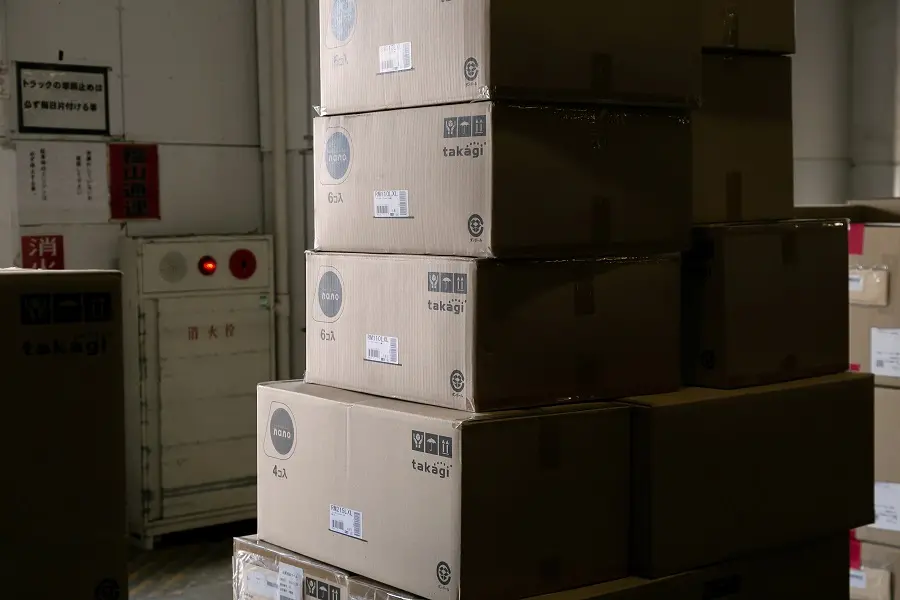
1961年に創業したタカギ。現在、園芸散水用品では国内トップシェア、蛇口一体型浄水器は新築マンションの導入率でトップです。ポリカンポンプから始まる、お客様に寄り添ったものづくりの精神は、今も変わらず受け継げられています。